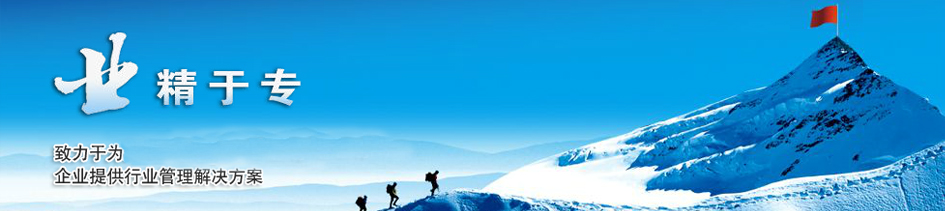
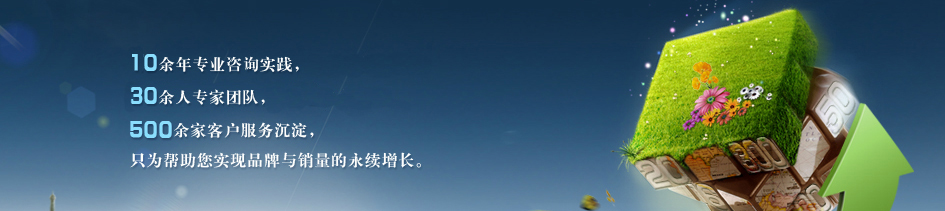
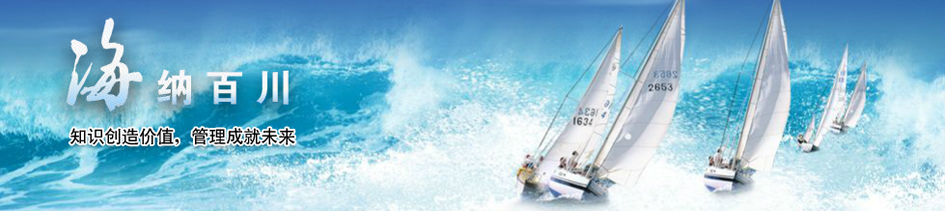
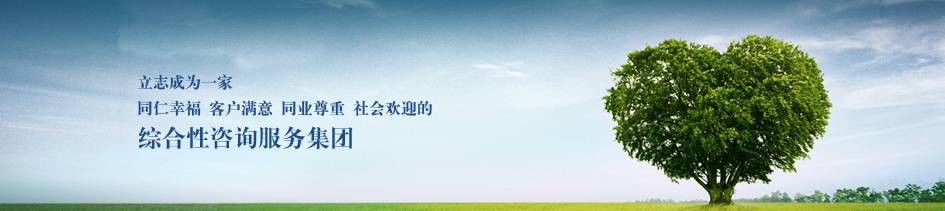

精益生產(chǎn)實(shí)戰(zhàn)訓(xùn)練
課程特色與背景
【課程目標(biāo)】
透過(guò)課程培訓(xùn),使學(xué)員了解掌握
— 精益基本理念、指導(dǎo)原則和運(yùn)作流程
—精益生產(chǎn)導(dǎo)入及實(shí)施策略
—看板系統(tǒng)的設(shè)計(jì)與運(yùn)用
— JIT生產(chǎn)排程技術(shù)和方法
—均衡生產(chǎn)與柔性制造技術(shù)
— 現(xiàn)場(chǎng)改善與目視化管理的方法
—幫助企業(yè)建立精益生產(chǎn)系統(tǒng),提高生產(chǎn)效率、降低成本、穩(wěn)定質(zhì)量、縮短生產(chǎn)周期,增強(qiáng)客戶滿意度,提升企業(yè)競(jìng)爭(zhēng)力
【課程大綱】
第一章、精益生產(chǎn)概述
一、精益生產(chǎn)與 TPS
二、精益誕生的背景與意義
三、人類工業(yè)化歷程的第三個(gè)里程碑
四、精益生產(chǎn)與大量生產(chǎn)
五、大野耐一的TPS理念
六、消除七大浪費(fèi)
七、精益生產(chǎn)終極目標(biāo)
八、精益企業(yè)的競(jìng)爭(zhēng)優(yōu)勢(shì)
九、我國(guó)精益管理發(fā)展趨勢(shì)
十、精益生產(chǎn)總體框架
第二章、TPS核心體系——準(zhǔn)時(shí)化與自動(dòng)化、準(zhǔn)時(shí)化(JIT)
一、什么是準(zhǔn)時(shí)化
1、快速響應(yīng)客戶的拉動(dòng)系統(tǒng)
2、前推式生產(chǎn)與后拉式生產(chǎn)
4、JIT按照節(jié)拍進(jìn)行生產(chǎn)
5、生產(chǎn)節(jié)拍與周期時(shí)間
6、建立流水線生產(chǎn)
7、一個(gè)流——JIT的高級(jí)形式
8、實(shí)現(xiàn)準(zhǔn)時(shí)化的前提條件
二、自動(dòng)化
1、什么是自働化?
2、賦予機(jī)器以人的智慧
3、自動(dòng)化目的和功能
4、自動(dòng)化規(guī)則及措施
5、準(zhǔn)時(shí)化與自働化的關(guān)系
精益生產(chǎn)案例
第三章、均衡化生產(chǎn)
一、龜兔賽跑——均衡化的意義
二、產(chǎn)生不均衡的原因
三、均衡化的內(nèi)容
四、均衡化生產(chǎn)的基礎(chǔ)
五、均衡化策略
六、如何實(shí)現(xiàn)混合生產(chǎn)排程
七、最終裝配過(guò)程均衡性的重要作用
八、均衡化的要領(lǐng)、優(yōu)勢(shì)與難點(diǎn)
第四章、看板系統(tǒng)的設(shè)計(jì)與運(yùn)用
一、看板的本質(zhì)
二、看板的功能與使用規(guī)則
三、看板的種類及式樣
四、看板運(yùn)用流程
五、設(shè)計(jì)和建立看板系統(tǒng)的步驟
六、看板設(shè)計(jì)的時(shí)機(jī)和條件
七、流程調(diào)查及分析
八、JIT中的戰(zhàn)略緩沖庫(kù)存
九、如何確定工作站周期時(shí)間
十、如何確定最小批量
十一、老化等待流程在制品限額
十二、計(jì)算看板的步驟和方法
十三、看板的簡(jiǎn)易計(jì)算
十四、看板的發(fā)行與維護(hù)
十五、看板的運(yùn)用方式及展示
十六、JIT生產(chǎn)計(jì)劃特點(diǎn)與組織方式
十七、Kanban系統(tǒng)與ERP的整合
案例分析
- 生產(chǎn)線看板運(yùn)作示范
- 貨倉(cāng)看板的運(yùn)作示范
- 供應(yīng)商看板運(yùn)作示范
第五章、標(biāo)準(zhǔn)作業(yè)
一、TPS標(biāo)準(zhǔn)作業(yè)的意義
二、標(biāo)準(zhǔn)作業(yè)三要素
三、標(biāo)準(zhǔn)作業(yè)制定
四、標(biāo)準(zhǔn)作業(yè)改善:SDCA與PDCA
五、編制QC工程表七大步驟及其應(yīng)用
六、豐田標(biāo)準(zhǔn)作業(yè)體系框架
七、豐田生產(chǎn)標(biāo)準(zhǔn)作業(yè)書實(shí)例
案例分析
第六章、TPS生產(chǎn)流程建立與優(yōu)化
一、生產(chǎn)系統(tǒng)布局的原則和方法
二、TPS與大量生產(chǎn)流程的區(qū)別
三、TPS生產(chǎn)布局與調(diào)整
四、柔性制造技術(shù)
五、U型生產(chǎn)單元
六、1人多工程與多能工培養(yǎng)
七、作業(yè)切換的原則與方法
八、縮短前置準(zhǔn)備時(shí)間的策略與方法
九、快速換模技術(shù)
十、不斷改進(jìn)流程(CIP)
案例分析
第七章、目視化管理
一、目視化管理的意義
二、建立標(biāo)準(zhǔn)
三、工廠布局應(yīng)考慮目視化因素
四、讓問(wèn)題無(wú)處可藏
五、發(fā)現(xiàn)和認(rèn)識(shí)問(wèn)題
六、反復(fù)“問(wèn)5個(gè)為什么”
七、使工作現(xiàn)場(chǎng)時(shí)刻處于受控狀態(tài)。
八、打好直觀工廠的基礎(chǔ)-5S
九、目視化管理的方式
十、管理信息透明化
十一、理想中的直觀工作區(qū)
十二、關(guān)于“直觀工廠”的研討
第八章、精益原理與改善策略
一、生產(chǎn)周期的概念
二、生產(chǎn)周期理論——利特爾定理
三、精益 思想及其五項(xiàng)原則
四、認(rèn)識(shí)和消除差異
1、質(zhì)量差異將導(dǎo)致缺陷或返工
2、時(shí)間差異將導(dǎo)致?lián)矶禄蜓诱`
3、精益意味著速度
4、縮短提前期的秘密武器——批量
5、精益三定理
6、精益改善策略
7、精益衡量指標(biāo)——流程周期效率
8、價(jià)值流圖分析
第九章、精益的支持保證基礎(chǔ)
一、觀念轉(zhuǎn)變——文化的力量
二、領(lǐng)導(dǎo)作用
三、TQM與質(zhì)量保證
四、自主管理與TEAM工作法
五、TPM全員設(shè)備維護(hù)
六、持續(xù)改善
第十章、精益生產(chǎn)導(dǎo)入與實(shí)施
一、精益生產(chǎn)方式導(dǎo)入藍(lán)圖
二、我國(guó)企業(yè)實(shí)施TPS的經(jīng)驗(yàn)教訓(xùn)
三、精益生產(chǎn)實(shí)施階段及步驟
四、策劃與準(zhǔn)備
五、精益管理分級(jí)培訓(xùn)
六、組建團(tuán)隊(duì)
七、精益項(xiàng)目管理
八、精益導(dǎo)入前期評(píng)估
九、確定精益實(shí)施目標(biāo)和方案
十、初級(jí)精益生產(chǎn)實(shí)驗(yàn)
十一、試點(diǎn)線選擇與切入
十二、5S:實(shí)施TPS的初級(jí)藍(lán)本
十三、總裝車間均衡化與看板實(shí)施
十四、公司精益生產(chǎn)體系全面展開(kāi)
十五、將供應(yīng)商納入公司精益體系
十六、精益生產(chǎn)總結(jié)與持續(xù)改進(jìn)
十七、精益項(xiàng)目咨詢策略
下一條:高效執(zhí)行力提升
上一條:企業(yè)管理診斷